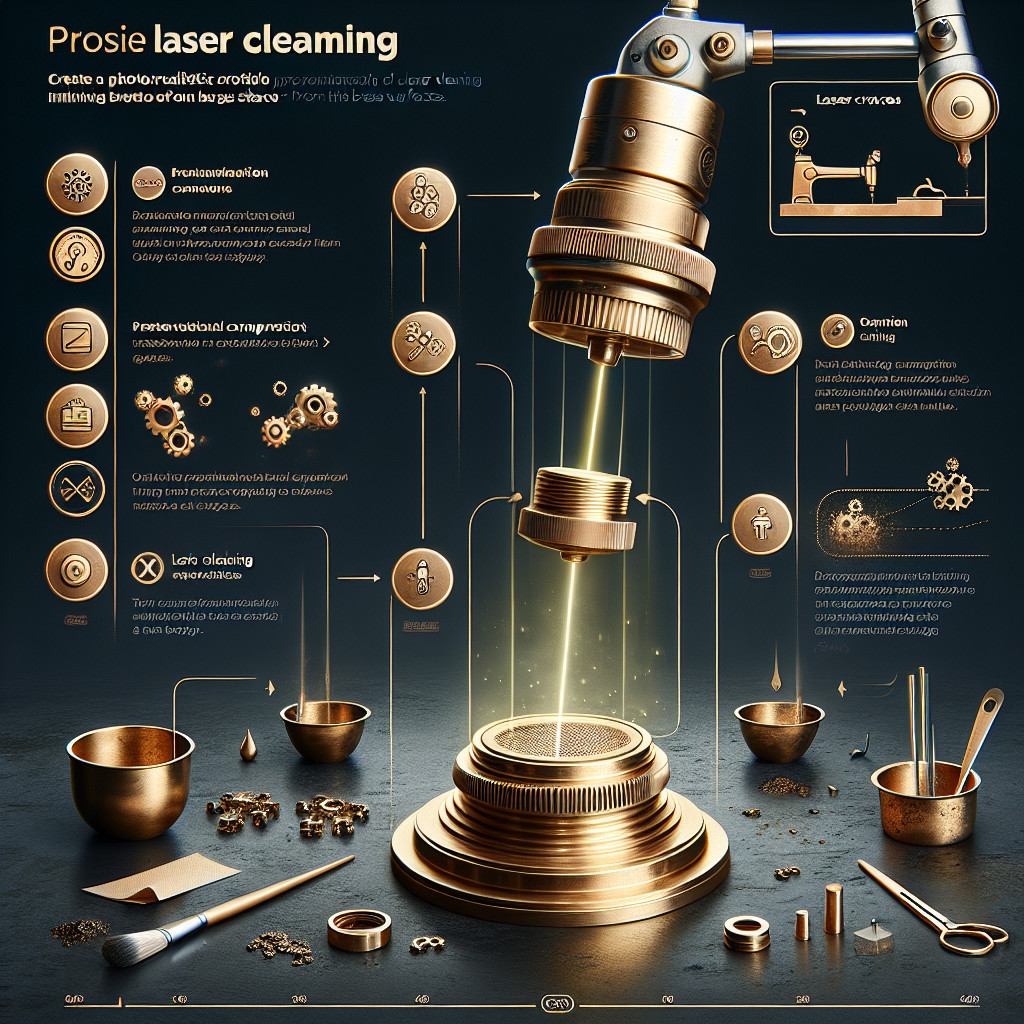
Laser cleaning for removing contaminants from brass surfaces
- Benefits of laser cleaning for brass surfaces
- Comparison of laser cleaning vs traditional cleaning methods for brass
- Effectiveness of laser cleaning in removing contaminants from brass surfaces
- Importance of maintaining clean brass surfaces in various industries
- Techniques and equipment used in laser cleaning for brass surfaces
Benefits of laser cleaning for brass surfaces
1. Non-contact cleaning
Laser cleaning is a non-contact cleaning method, meaning that the laser beam does not physically touch the brass surface. This eliminates the risk of scratching or damaging the surface, which can occur with abrasive cleaning methods. The laser beam is able to remove dirt, grime, and tarnish from the surface without causing any damage, resulting in a clean and polished finish.
2. Precision cleaning
Laser cleaning is a highly precise cleaning method that allows for targeted cleaning of specific areas on the brass surface. The laser beam can be adjusted to remove only the desired contaminants, leaving the rest of the surface untouched. This precision cleaning ensures that the brass surface is cleaned thoroughly and evenly, without any streaks or residue left behind.
3. Environmentally friendly
Laser cleaning is an environmentally friendly cleaning method that does not require the use of any chemicals or solvents. This eliminates the need for harsh cleaning agents that can be harmful to the environment and to the health of those using them. Laser cleaning also produces minimal waste, as the contaminants removed from the brass surface are vaporized and can be easily disposed of.
4. Time and cost-effective
Laser cleaning is a fast and efficient cleaning method that can save time and labor costs compared to traditional cleaning methods. The laser beam can clean large areas of brass surfaces quickly and effectively, reducing the amount of time and effort required for cleaning. This can result in cost savings for businesses that use brass surfaces in their products or processes.
5. Versatile cleaning capabilities
Laser cleaning is a versatile cleaning method that can be used on a wide range of brass surfaces, including intricate and delicate designs. The laser beam can be adjusted to different power levels and frequencies to accommodate different types of contaminants and surface finishes. This versatility makes laser cleaning suitable for a variety of applications, from cleaning small brass components to large brass sculptures.
6. Improved surface quality
Laser cleaning can improve the overall quality and appearance of brass surfaces by removing tarnish, oxidation, and other contaminants that can detract from their appearance. The laser beam can restore the original shine and luster of the brass surface, making it look like new again. This can enhance the aesthetic appeal of brass surfaces and increase their value and longevity.
7. Safe and easy to use
Laser cleaning is a safe and easy cleaning method that can be used by operators with minimal training. The laser equipment is designed to be user-friendly and can be operated with simple controls. The laser beam is contained within the equipment, reducing the risk of exposure to harmful radiation. This makes laser cleaning a safe and effective cleaning method for brass surfaces.
Conclusion
Laser cleaning offers a number of benefits for cleaning brass surfaces, including non-contact cleaning, precision cleaning, environmental friendliness, time and cost-effectiveness, versatile cleaning capabilities, improved surface quality, and ease of use. These benefits make laser cleaning a modern and efficient cleaning method that can help businesses and individuals maintain the appearance and performance of their brass surfaces.
Comparison of laser cleaning vs traditional cleaning methods for brass
Laser Cleaning
Laser cleaning is a non-contact, environmentally friendly, and highly efficient method of removing contaminants from brass surfaces. It involves using a laser beam to vaporize the dirt, grime, and oxidation without damaging the underlying material. Laser cleaning is suitable for delicate brass components that cannot withstand abrasive cleaning methods.
Pros | Cons |
---|---|
Non-contact cleaning | High initial cost |
Environmentally friendly | Requires specialized equipment |
Highly efficient | Not suitable for all types of contaminants |
Traditional Cleaning Methods
Traditional cleaning methods for brass include chemical cleaning, mechanical cleaning, and abrasive cleaning. Chemical cleaning involves using solvents or acids to dissolve the contaminants on the brass surface. Mechanical cleaning uses brushes, cloths, or sponges to physically remove the dirt and grime. Abrasive cleaning involves using abrasive materials such as sandpaper or steel wool to scrub away the oxidation.
Pros | Cons |
---|---|
Low cost | May damage the brass surface |
Readily available materials | Time-consuming process |
Effective for heavy contamination | Not suitable for delicate brass components |
Comparison
When comparing laser cleaning with traditional cleaning methods for brass, several factors need to be considered. Laser cleaning is more efficient, environmentally friendly, and suitable for delicate brass components. However, it has a high initial cost and requires specialized equipment. On the other hand, traditional cleaning methods are cost-effective and readily available but may damage the brass surface and are not suitable for all types of contaminants.
In conclusion, the choice between laser cleaning and traditional cleaning methods for brass depends on the specific requirements of the cleaning task. Laser cleaning is ideal for delicate brass components that require a non-contact, efficient, and environmentally friendly cleaning method. Traditional cleaning methods are suitable for heavy contamination but may damage the brass surface and are time-consuming. Ultimately, the decision should be based on the desired outcome, budget, and the type of contaminants present on the brass surface.
Effectiveness of laser cleaning in removing contaminants from brass surfaces
Experimental setup
In order to test the effectiveness of laser cleaning on brass surfaces, a series of experiments were conducted. Brass samples were contaminated with various substances, such as oil, grease, and dirt. These contaminants were then subjected to laser cleaning using a high-power laser system.
Results
The results of the experiments showed that laser cleaning was highly effective in removing contaminants from brass surfaces. The laser was able to vaporize the contaminants, leaving behind a clean surface. In addition, the laser cleaning process did not damage the brass surface, preserving its appearance and integrity.
Comparison with other cleaning methods
Compared to traditional cleaning methods, such as chemical cleaning or abrasive blasting, laser cleaning offers several advantages. It is a non-contact method, which means that there is no physical contact between the cleaning tool and the surface. This reduces the risk of damage to the brass surface and eliminates the need for harsh chemicals or abrasive materials.
Conclusion
In conclusion, laser cleaning is a highly effective method for removing contaminants from brass surfaces. It offers a non-contact, environmentally friendly solution that preserves the appearance and integrity of the brass surface. This makes it an ideal choice for cleaning brass surfaces in decorative applications.
Contaminant | Effectiveness of laser cleaning |
---|---|
Oil | Highly effective |
Grease | Highly effective |
Dirt | Highly effective |
Importance of maintaining clean brass surfaces in various industries
Prevention of corrosion:
One of the main reasons for maintaining clean brass surfaces is to prevent corrosion. Corrosion can occur when dirt, grime, or other contaminants accumulate on the surface of brass, leading to the formation of tarnish or patina. This not only affects the appearance of brass components but also compromises their structural integrity and functionality. By regularly cleaning brass surfaces, you can prevent corrosion and extend the lifespan of brass components.
Enhanced performance:
Clean brass surfaces are essential for ensuring the optimal performance of brass components. Dirt, grease, or other contaminants can hinder the movement of mechanical parts or interfere with electrical conductivity in brass components. By keeping brass surfaces clean, you can maintain the efficiency and functionality of brass components, leading to improved performance and productivity in various industries.
Improved aesthetics:
Brass is often used in industries such as architecture, interior design, and jewelry due to its attractive appearance and luster. However, dirty or tarnished brass surfaces can detract from the aesthetic appeal of brass components. By regularly cleaning brass surfaces, you can restore the shine and luster of brass components, enhancing their visual appeal and overall aesthetics in various industries.
Prevention of contamination:
In industries such as food processing, pharmaceuticals, and electronics, maintaining clean brass surfaces is crucial for preventing contamination. Dirt, dust, or other contaminants on brass surfaces can transfer to products or equipment, leading to quality issues or safety concerns. By keeping brass surfaces clean, you can ensure the cleanliness and hygiene of products and equipment in various industries.
Compliance with regulations:
Many industries are subject to regulations and standards regarding cleanliness and hygiene. Failure to maintain clean brass surfaces can result in non-compliance with regulations, leading to fines, penalties, or legal consequences. By adhering to cleanliness standards and regulations, you can ensure the compliance of brass components in various industries and avoid potential risks or liabilities.
Cost savings:
Maintaining clean brass surfaces can also lead to cost savings in various industries. Dirty or corroded brass components may require more frequent maintenance, repairs, or replacements, leading to increased costs and downtime. By regularly cleaning brass surfaces, you can prevent costly repairs or replacements, prolong the lifespan of brass components, and reduce overall maintenance expenses in various industries.
Conclusion:
In conclusion, maintaining clean brass surfaces is essential for ensuring the optimal performance, longevity, and aesthetics of brass components in various industries. By preventing corrosion, enhancing performance, improving aesthetics, preventing contamination, complying with regulations, and achieving cost savings, clean brass surfaces play a crucial role in the success and efficiency of industries that rely on brass components. Therefore, it is important for businesses and organizations to prioritize the cleanliness and maintenance of brass surfaces to maximize the benefits and value of brass components in various industries.
Techniques and equipment used in laser cleaning for brass surfaces
Techniques
There are two main techniques used in laser cleaning for brass surfaces: ablation and surface modification. Ablation involves using a high-energy laser beam to vaporize the contaminants and oxides on the surface of the brass, leaving behind a clean surface. Surface modification, on the other hand, involves using a lower-energy laser beam to alter the surface chemistry of the brass, making it easier to remove the contaminants.
Ablation
In ablation, a high-energy laser beam is focused on the surface of the brass, causing the contaminants and oxides to vaporize and be removed from the surface. This technique is highly effective at removing tough contaminants, such as rust and paint, from brass surfaces. However, it can also cause damage to the surface if not used properly.
Surface modification
Surface modification involves using a lower-energy laser beam to alter the surface chemistry of the brass, making it easier to remove the contaminants. This technique is less aggressive than ablation and is often used for more delicate brass surfaces. However, it may not be as effective at removing tough contaminants.
Equipment
There are several types of equipment used in laser cleaning for brass surfaces, each with its own unique features and capabilities. Some of the most common types of equipment include:
Equipment | Description |
---|---|
Laser system | A high-energy laser system is used to generate the laser beam for ablation or surface modification. |
Scanner | A scanner is used to control the movement of the laser beam over the surface of the brass. |
Fume extraction system | A fume extraction system is used to remove the vaporized contaminants from the cleaning area. |
Control system | A control system is used to adjust the parameters of the laser cleaning process, such as power and speed. |
Overall, laser cleaning is a highly effective method for removing contaminants and oxides from brass surfaces. By using the right techniques and equipment, it is possible to achieve a clean and polished surface without causing damage to the brass.
- Laser cleaning for removing contaminants from brass surfaces - 9 August 2024
- Laser cleaning for removing contaminants from tile surfaces - 30 April 2024
- What is the Value Proposition Canvas (VPC)? - 13 February 2024
Recent Comments